The production of women’s sanitary napkins involves precise processes, high-quality raw materials, and specialized machinery to ensure comfort, absorbency, and hygiene. Below is a detailed breakdown of the manufacturing process and essential factors for setting up a production line.
1. Raw Material Preparation
Sanitary napkins are composed of multiple layers, each serving a specific function:
Top Sheet (Non-Woven Fabric or Perforated PE Film) – Provides a soft, skin-friendly surface for quick liquid absorption.
Absorbent Core (Fluff Pulp + Super Absorbent Polymer/SAP) – Enhances liquid retention and prevents leakage.
Back Sheet (Polyethylene/PE Film) – Acts as a waterproof barrier.
Adhesives (Hot Melt Glue) – Bonds the layers together securely.
Packaging Materials – Individual wraps (cast film or non-woven) and outer bags (aluminum foil or PE plastic).
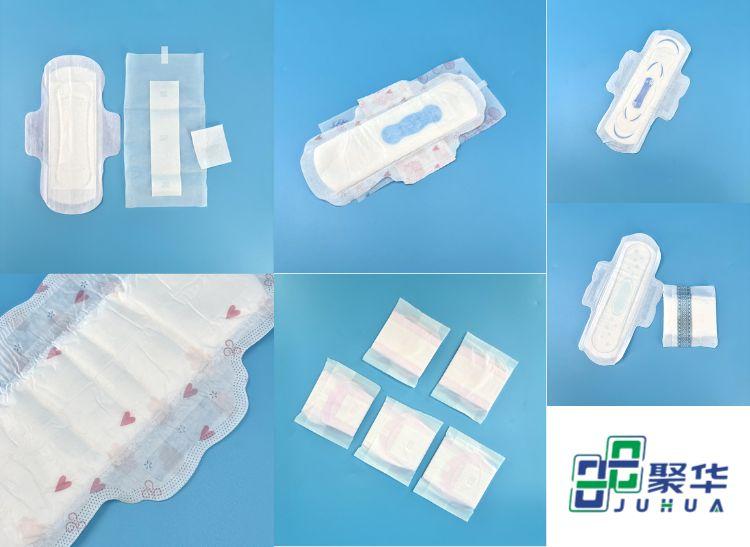
2. Fiber Processing & Core Formation
The fluff pulp is mechanically crushed to improve fiber structure, enhancing absorbency and softness.
SAP (Super Absorbent Polymer) is mixed with the pulp to maximize liquid retention.
3. Sanitary Napkin Assembly
The absorbent core (pulp + SAP) is sandwiched between the top sheet and back sheet.
Hot melt glue is applied to bond the layers securely.
The napkin is shaped (regular, ultra-thin, or winged) and sealed with side leak-proof barriers (PE film or elastic edges).
4. Packaging & Final Quality Checks
Each napkin is individually wrapped with an easy-peel adhesive tape for hygiene.
Multiple napkins (typically 8 or 10 per pack) are packed into aluminum foil or PE plastic bags for retail distribution.
Quality control ensures absorption capacity, dryness, and durability meet industry standards.A fully automated sanitary napkin production line can achieve speeds of 800–900 pieces per minute.